HGM series of three-rings and medium-speed micro powder grinder is a new type of making micro powder machines through more than twenties times research and improvement, depending on two decades of hard work & experience and inputting the latest mechanical techniques of Sweden. It is an incorporated one of the two countries and a leader of the grinding industry nowadays. 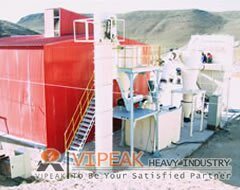 Usage: HGM series of three-rings and medium-speed micro powder grinder is widely used in making fine powder or micro powder, and the raw materials should be non-inflammable and non-explosive under the Moh's hardness less than 6 grade such as limestone, calcite, dolomite, kaolin, bentonite, talc, illite, pyrophillite, barite, meerschaum, fluorite, potash ore, etc. The lifetime of spare parts is relied on the hardness of raw materials, and is lowered once the Moh's hardness is up to 4-6 grade.
Working principle: The mainframe through reducer makes the main shaft and all the turntables rotating which lets the rollers and the ring rolling and rotating with dowel pin. First the large ones of the materials is crushed into small ones by the hammer crusher and the later is transmitted into the hopper by elevator, then the vibrating feeder sends the materials onto the middle of the upper turntable in a stable and well-proportioned way, which are separated under the centrifugal force and fall into the raceway where they are crushed, grinded, rolled. Through the first process, enter into the second turntable then the third one. Hyper centrifuger indrafts the air inside and carries the larger powder into the collecting powder machine. The vortex made by rotating turbine of the collecting powder machine lets the larger ones recycled back into the grinding chamber for regrinding, then smaller ones enter into the cyclone collector and final products are discharged by the valve, airflow with little fine dust is refined by pulse dust catcher and discharged through the blower and the muffler. Main features: 1, High efficiency and lower consumption. In the condition of the same material, power and the fineness, its capacity is increased by 40% compared to the jet mill and mixing grinder. 2, Longevity. In the condition of the same power and the fineness, the spare parts have a longer lifetime, usually more than one year, to the shaft impactor crusher and the turbine crusher. 3, Non-bearings and non-bolt in the grinding chamber. Because of this, these questions destroying the machines can never exist for bearing, sealing element or the bolts loose. 4, The fineness of final products can add up 5μm, and screening rate is 97%. specification and technical parameter
Model |
Average Diam-eter (mm) |
No. of Roller and Ring |
The Feeding Size (mm) |
Size of Finished Product |
Capacity (kg/h) |
Motor Power (kw) |
Dimension (L×W×H) (m) |
Weight of Main Milland Classifier (kg) |
Roller (Pcs) |
Ring (Pcs) |
Micron |
Mesh |
MainMill |
Class-ifier |
AirB-lower |
Vibrating Feeder |
Discharge Valve |
HGM60 |
600 |
15 |
2 |
≤10 |
5-47 |
3250-325 |
350-2500 |
37 |
11 |
30 |
0.06 |
0.75 |
10×3×5.5 |
5200 |
HGM80 |
800 |
21 |
2 |
≤10 |
5-47 |
3250-325 |
600-4000 |
75 |
22 |
45 |
0.06 |
0.75 |
11.9×2.7×5.8
|
7000 |
HGM100 |
1000 |
27 |
2 |
≤10 |
5-47 |
3250-325 |
900-6000 |
90 |
30 |
75 |
0.15 |
1.1 |
15.5×4.5×8.6 |
9500 |
|